Blog NR12SemSegredos
Segurança em primeiro lugar

3 passos para fazer uma Análise de Risco e atender a NR12
3 passos para fazer uma Análise de Risco e atender a NR12
Para evitar um acidente, a coisa mais importante a se fazer é analisar os riscos envolvidos, usando as habilidades de um profissional, usando critérios normatizados e incluindo na análise possibilidades reais.
Se você já se deparou com a pergunta: Apreciação, Avaliação ou Análise de Risco? Acredito que esta explicação vai ajudar a entender a diferença.
Geralmente é utilizado Análise para uma Apreciação, e vice-e-versa, e se você buscar no dicionário as palavras são sinônimas, mas para efeito de Segurança em máquinas podemos utilizar as definições dada pela NBR ISO 12100 em seu glossário.
Análise de Risco: Combinação da especificação dos limites da máquina, identificação dos perigos e estimativa dos riscos
Avaliação de Risco: Julgamento com base na análise de risco, do quanto os objetivos de redução de risco foram atingidos
Apreciação do risco: Processo completo que compreende a análise de risco e avaliação de risco
A diferença é sutil, mas pode ser utilizado como referência o gráfico abaixo, dependendo do estágio que se está realizando o trabalho de adequação à NR12.
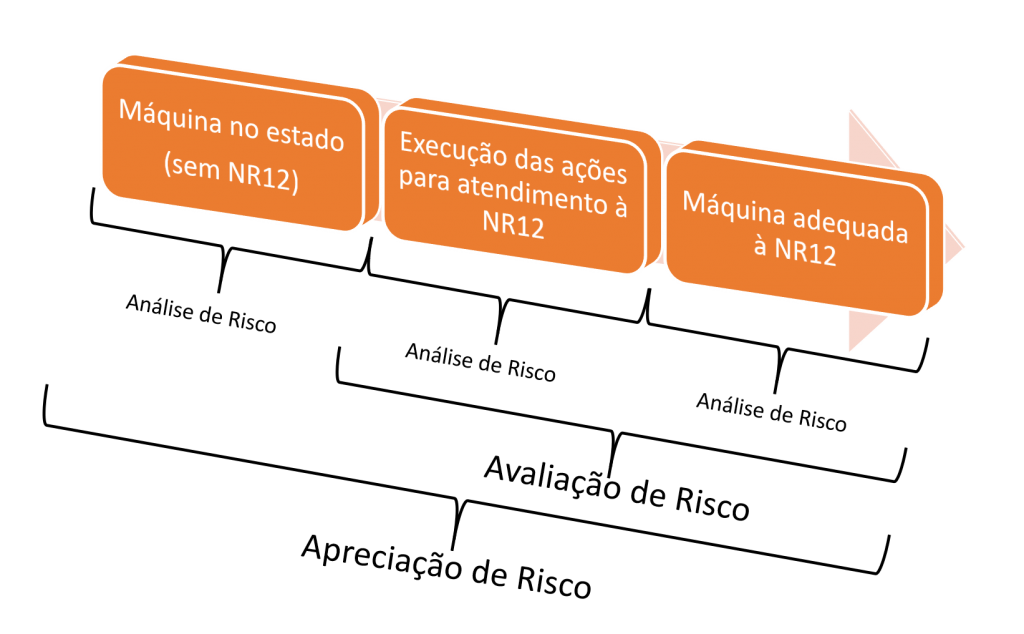
A NR12 exige que a máquina tenha uma análise de risco, e isto pode ser visto no item 12.39(a) e em outros é referenciado à este documento como base para realização do item. A norma técnica vigente que indica a realização do procedimento é a NBR ISO 12100:2013
Mas qual é mesmo o objetivo da NR12?
Você pode ter imaginado que a necessidade de segurança em máquina iniciou na publicação da norma, mas isso não está correto. Vou explicar porque, as Normas Regulamentadoras, foram publicadas para ajudar a explicar pontos da lei, que são muito genéricos, ajudando ao atendimento à lei. No caso da NR12, ela foi elaborada para regulamentar os Art. 184, 185 e 186 da CLT, que traz no seu texto as seguintes redações (CLT, 1943):
“Art. 184 – As máquinas e os equipamentos deverão ser dotados de dispositivos de partida e parada e outros que se fizerem necessários para a prevenção de acidentes do trabalho, especialmente quanto a risco de acionamento acidental;”
Parágrafo único – É proibida a fabricação, a importação, a venda, a locação e o uso de máquinas e equipamentos que não atendam ao disposto neste artigo.
“Art. 185 – Os reparos, limpeza e ajustes somente poderão ser executados com as máquinas paradas, salvo se o movimento for indispensável à realização ao ajuste;”
“Art. 186 – O Ministério do Trabalho estabelecerá normas adicionais sobre proteção e medidas de segurança na operação de máquinas e equipamentos, especialmente quanto à proteção das partes móveis, distância entre estas, vias de acesso às máquinas e equipamentos de grandes dimensões, emprego de ferramentas, sua adequação e medidas de proteção exigidas quando motorizadas ou elétricas”.
Fonte: Planalto Brasileiro (http://www.planalto.gov.br/ccivil_03/decreto-lei/Del5452compilado.htm)
Os 3 Passos para fazer uma Análise de Risco:
1- Determinação dos Limites da Máquina
Para a determinação dos limites da máquina deve-se levar em consideração de todas as fases do ciclo de vida da máquina (projeto, construção, transporte, montagem, instalação, operação, limpeza, setup, manutenção, desativação, desmontagem, descarte).
O limite é basicamente a utilização principal da máquina, e para efeito de concepção da máquina e análise de risco deve ser considerado a utilização normal e os maus usos razoavelmente previsíveis. Então para facilitar segue uma lista de itens que compõem a determinação do limite da máquina:
Limite de uso
– Diferentes modos de operação
– Manutenção da máquina (desgaste e mau uso)
– Tipo de utilização se é industrial ou residencial
– Identificação do operador como gênero, idade, mão de uso dominante, e se possível utilização por pessoas com habilidades reduzidas (visual, auditiva, tamanho, força e outras)
– Nível de treinamento, habilidade e experiência necessário para utilização e manutenção
– Exposição de outras pessoas aos perigos relacionadas à máquina que sejam razoavelmente previsíveis
Limite de espaço
– Movimentos da máquina e cursos dos movimentos
– Espaços de uso do operador e manutenção
– Qual tipo de interação do operador à máquina
– Conexões de energia (elétrica, hidráulica, mecânica, gravitacional e outras)
Limites de tempo
– Vida útil da máquina considerando o uso normal ou mau uso razoavelmente previsível
– Intervalos de manutenção recomentado
Outros limites
– tipos de materiais e matéria prima processados
– limpeza e manutenção diária do equipamento
– organização do trabalho
– ambiente (umidade, particulados, altitude, agentes químicos e outros)
2- Identificar os Perigo e Risco
Depois de determinado os limites da máquina a identificação dos perigos e riscos existentes devem ser feitas utilizando os seguintes critérios:
– Uso normal do equipamento
– Mau uso razoavelmente previsível
Estes perigos podem estar em qualquer etapa do ciclo de vida da máquina:
(projeto, construção, transporte, montagem, instalação, operação, limpeza, setup, manutenção, desativação, desmontagem, descarte).
A lista de perigo é o Anexos B da NBR12100, e são separados por tipos, origem, consequências e referenciais para normas internacionais.
Na elaboração desta lista de perigos existente é importante que o profissional se atente às operações possíveis da máquina, incluindo:
Ajustes;
Testes;
Programação / parametrização;
Trocas de ferramentas/moldes;
Partida inicial/ colocação em marcha / Startup
Partidas/Pausas
Modo de operação manual/ automático / ciclo lento
Parada de emergência
Reinicio de operação após bloqueio de emergência
Processo de Lockout/Tagout
Limpeza e organização
Manutenção preventiva/corretiva
Manutenção diária
Rotinas e procedimentos do processo
Alimentação/Descarga da matéria prima
Deve ser considerado também os Comportamentos da máquina em ações não intencionais do operador ou formas de mau uso razoavelmente previstas.
2- Estimativa do risco
O risco associado a uma situação perigosa depende de fatores como:
– Gravidade do dano no caso de um acidente
– Probabilidade de ocorrência (exposição, ocorrência do perigo e possibilidade de evitar)
Um método muito comum de se utilizar para fazer esta estimativa é o HRN (Hazard Rating Number) em português seria algo como: Valor de Classificação de Risco
O HRN expressa em valor numérico o risco para um determinado perigo/situação, desta forma podemos transformar a medida qualitativa em quantitativa, ou seja, um número.
Para conseguir chegar no HRN de uma situação/perigo devemos calcular seguindo a fórmula?
HRN=PExFExGPDxNP
considerando-se:
(PO) à Probabilidade de Ocorrência do Dano
(FE) à Frequência de Exposição ao Perigo/Risco
(GPD) à Gravidade da Possível Lesão
(NP) à Número de Pessoas Expostas
Vou detalhar agora cada um dos itens:
(PO) à Probabilidade de Ocorrência do Dano
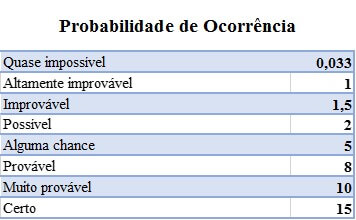
(FE) à Frequência de Exposição ao Perigo/Risco
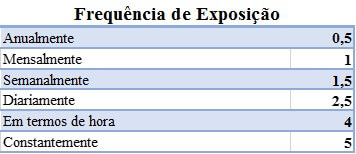
(GPD) à Gravidade da Possível Lesão
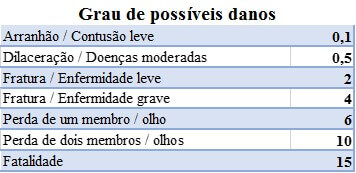
(NP) à Número de Pessoas Expostas
E como resultado temos da fórmula (HRN=PExFExGPDxNP), a tabela identificará o valor e resultado:
Uma tabela como essa deverá seu o resultado deste trabalho:
Colocar em prática
Quanto você utilizar estes passos para realizar a Análise de Risco, você vai completar uma importante etapa para o atendimento da NR12 em uma máquina. Pois com este trabalho você terá um mapa com os pontos mais críticos que podem ser priorizados e atacados com mais assertividade.
O processo de Análise de Risco deve contar com um profissional experiente no processo e no equipamento, para que ele seja capaz de identificar riscos que normalmente não seriam apontados por alguém leigo no processo.
Aproveite para conhecer nosso conteúdo NR12SemSegredos:
33 comentários em “3 passos para fazer uma Análise de Risco e atender a NR12”
Alexandre Dias
Boa noite Douglas, estou pós graduando em engenharia de segurança do trabalho e meu tcc será exatamente sobre apreciação de riscos a nr-12, em qual norma posso me referenciar para o calculo da estimativa do risco? me recomenda alguma norma a mais? estou usando a nr-12, a nbr14154, nbr iso 12100. agradeço a atenção
ERNANI NICOMEDES
BOM DIA !
Muito bom este material, parabéns pela apresentação do assunto da NR-12.
André Oliveira de Oliveira
Douglas, um mito da NR12
Jesimiel
Muito bom artigo. A falta desta análise é um pressupostos do grande número de acidente com máquinas e equipamentos.
Alexandre LIMA Rodrigues
Muito boa analise, acredito que seja um exemplo a ser seguido.
Diego Faria
Quem pode fazer a APR para NR12?
Douglas Custodio
A APR deve ser elaborada por um profissional habilitado pela sua formação, e com conhecimento no processo que está sendo analisado, principamente nos riscos.
FRANCISCO COSMO
Boa tarde senhores.
APR deve ser elaborado por uma comitiva, não só por pessoais habilitado por formação técnica; como também pessoais pratica; senhores quem tem vivência pratica com equipamento, enxerga mais um pouco, não tirando o mérito do profissional habilitado.
Monique
Alguém recebeu esses modelo de Análise de Risco de Equipamento?
Gostaria também de receber [email protected]
andrezza hayden
Prezados,
Preciso de um modelo de inventário de maquinas e equipamentos e também um modelo de check list de maquinas. Quem puder ajudar, agradeço.
Att,
Alex Mendes de Aguiar
Boa noite Andrezza
Já conseguiu os modelos que precisava ?
Everton Araújo
Alex, boa tarde!
Poderia me disponibilizar esses modelos?
Marcelo Oliveira
Se puder também gostaria de recebê-los.
SAMUEL RODRIGUES DE ALENCASTRO
Alex, boa tarde!
Gostaria de receber esses modelos também, por gentileza.
ALVARO CABRAL DE CASTILHO NETO
BOA TARDE Alex Mendes de Aguiar , SERÁ QUE VC TBEM TEM UM MODELO DE ANALISE DE RISCO DE MÁQUINAS (NR-12);
OBRIGADO
vitor silva bispo
Boa tarde, tbm gostaria de receber os modelos. [email protected]
Pablo Conceição
Caros colegas, tenho uma planta de filtração de água composta por 4 skids (uma unidade de bombeio, uma unidade de filtros de sólidos, uma unidade de floculação química e uma unidade de manifold de distribuição). No enquadramento à NR12, posso emitir uma ART para todo o sistema ou tenho que emitir uma ART para cada um dos 4 skids? OBS: Os skids só operam interligados uns aos outros. Obrigado a quem puder ajudar.
Douglas Custodio
Não é a NR12 que definirá a quantidade e formato de ART, mas o CREA. Sugiro verificar com o CREA do seu estado como proceder neste caso.
Lembre que ART é somente a individualização da responsabilidade técnica (por um trabalho executado). Não existe uma ART para NR12, e sim ART para atividades de atendimento à Norma.
JOAO CARLOS PIRES CAMPOS
A futura alteração da NR 12 deverá simplificar a Análise de Riscos para processos como este que você está apresentando. Você deve emitir uma ART para cada serviço realizado, se as quatro unidades estão contemplados em um único serviço (Planta de Filtração de Água) basta uma ART. A ART é um documento do profissional e garante seu acervo profissional.
thiago
Boa Tarde Douglas.
Uma Dúvida, Sou engenheiro elétrico posso realizar á analise de risco de máquinas e equipamentos com emissão de ART sobre NR 12 da empresa que trabalho ou tenho que ser graduado com Titulo de Engenheiro de Segurança do Trabalho?
JOAO CARLOS PIRES CAMPOS
A análise de riscos de máquinas é de competência do PLH em Engenharia de Segurança do Trabalho. Ao engenheiro Eletricista compete o projeto e coordenação dos trabalhos da parte dos circuitos elétricos (comando e força) das máquinas. Cada um dentro de seus limites de competência/habilitação.
carlos ezequiel
Excelente post
JOÃO BATISTA
Caros Senhores
Qual a norma que fornece a PO a FE a GPD a NP e o HRN?
Felipe
RESOLUÇÃO 218/73 CONFEA
Art. 12 – Compete ao ENGENHEIRO MECÂNICO ou ao ENGENHEIRO
MECÂNICO E DE AUTOMÓVEIS ou ao ENGENHEIRO MECÂNICO E DE ARMAMENTO ou
ao ENGENHEIRO DE AUTOMÓVEIS ou ao ENGENHEIRO INDUSTRIAL MODALIDADE
MECÂNICA:
I – o desempenho das atividades 01 a 18 do artigo 1º desta Resolução, referentes
a processos mecânicos, máquinas em geral; instalações industriais e mecânicas; equipamentos
mecânicos e eletro-mecânicos; veículos automotores; sistemas de produção de transmissão e de
utilização do calor; sistemas de refrigeração e de ar condicionado; seus serviços afins e correlatos.
A SABER:
Atividade 02 – Estudo, planejamento, projeto e especificação;
Atividade 06 – Vistoria, perícia, avaliação, arbitramento, laudo e parecer técnico;
Atividade 11 – Execução de obra e serviço técnico;
Portanto, embora a RESOLUÇÃO Nº 359, DE 31 JUL 1991. de atribuições ao eng. de segt, o eng. mecânico também é habilitado a realizar apreciações de riscos, projetar e adequar equipamentos e máquinas de acordo com a NR-12.
Leonardo Augusto da Silva
Bom dia, teria a possibilidade de me enviar o material completo referente a Análise de Riscos para Atendimento a NR12, por gentileza?
Leonardo Augusto da Silva
Bom dia, teria a possibilidade de me enviar o material completo referente a Análise de Riscos para Atendimento a NR12, por gentileza?
Marlei Gomes Ferreira Brant
Bom dia Pessoal!
Vocês podem me mandar o modelo da análise de risco de equipamentos?
Agradecida.
[email protected]
Roberto
Saudações Pessoal!
Vocês podem me mandar o modelo da análise de risco de equipamentos
Clininey
Douglas vc pode disponibilizar uma planilha de analise de risco pra mim ?
Afrânio da Silva viana
Prezados,
Preciso de um modelo de inventário de maquinas e equipamentos e também um modelo de check list de maquinas. Quem puder ajudar, agradeço.
Att,
Walter de Oliveira
Em uma planta completa de produção com vários equipamentos e diferentes fornecedores de máquinas e sistemas, de quem é a responsabilidade de realizar a apreciação de riscos?
– Do fornecedor do Projeto Basico e Tecnologia do Processo?
Do fornecedor do Projeto de Detalhamento Mecânico?
Do proprietário da Investimento?
Do principal fornecedor dos equipamentos?
Douglas Custodio
A responsabilidade é de cada uma das áreas envolvidas, mas vai existir um profissional que reunirá todas essas informações para uma tomada de ação. Mas se sua pergunta é quem deveria “pagar” por esse trabalho, imagino que em cada empresa tenha pontos de vistas diferentes, eu particularmente acho que é o proprietário da máquina, pois é ele quem assume a responsabilidade civil (ou criminal se for considerado assim) por um acidente.